Aerial Survey of Kinshasa, DRC
- Luke Wijnberg
- Oct 1, 2021
- 3 min read
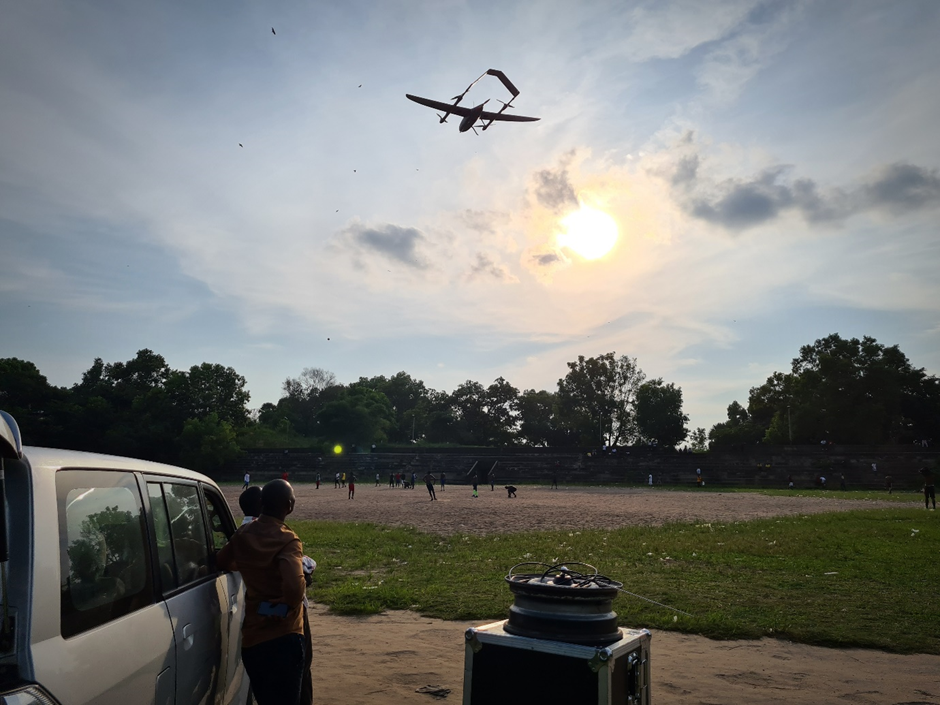
3DroneMapping undertook an aerial survey of a site along the Ndjili River, Kinshasa in the Democratic Republic of the Congo. The project comprised a total surface area of approximately 10 000 hectares. The client requested orthomosaics and DTM products be produced.
Various ground control points / markers were required for the aerial survey of an area. These needed to be established and coordinated as well as additional quality checkpoints. Each control point was to be surveyed to within 20mm accuracy or better. Additional points were collected to aid the accuracy of the point cloud registration. These included road markings, spot levels and other points that could be interrogated during the photogrammetric processes. These points will form part of the secondary control points to check on the accuracy derived from the primary control points.

Effective data capture for this project necessitated the use of a fixed wing drone. Since these typically require a large flat runway to take off and land, a futile attempt was made to locate such a place near the area of interest. Finding a secure, empty and obstruction free area in densely populated Kinshasa was a very tall order and none could be located. It was decided to rather change to a slightly less efficient airframe that can take off and land vertically but can transition into fixed wing flight for greater efficiency. Such an aircraft is called a VTOL (Vertical Take-off and Landing)
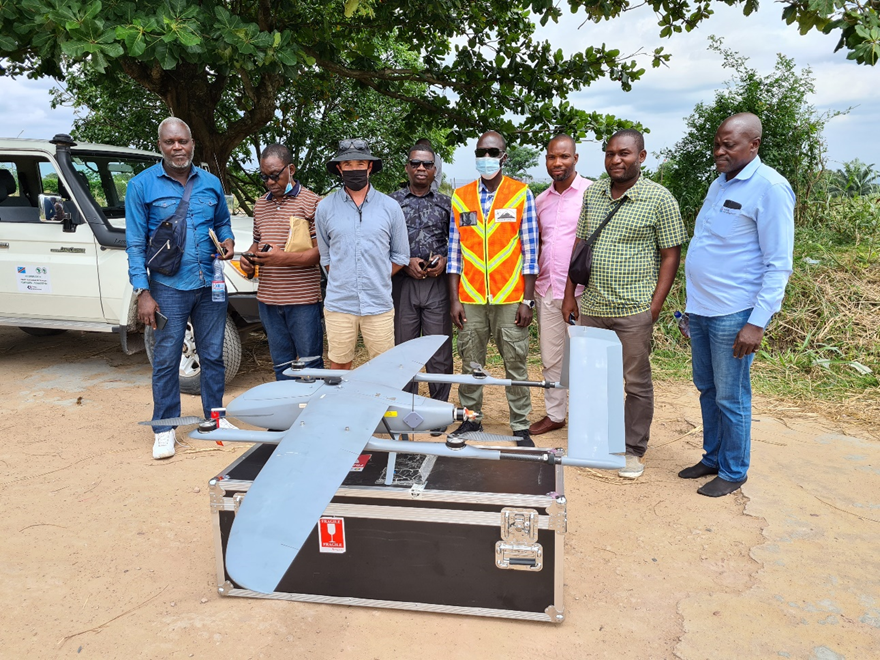
Since the Civil Aviation Authority required certain technologies to work in controlled airspace, additional safety features were added to the airframe such as Automatic Dependent Surveillance–Broadcast (ADS-B) which allows for all aircraft to locate each other, strobe lighting and automated avoidance systems.
The aircraft used was of our own 3DroneMapping design and built by our inhouse Research & Development team. In addition to the required safety equipment, the airframe was equipped with long range communications (C2 or command and control) systems, high-capacity dual power delivery mechanisms, and multiple redundancy control surfaces.
The aerial survey componentry consisted of a calibrated metric camera with 60MP sensor and a INS system. The INS is composed of a dual frequency L1/L2 multi-constellation receiver and Inertial Measuring Unit (IMU). These units are capable of measuring angles and positions up to 400 times a second to within 1cm in terms of position and 0.004 ° in terms of pitch, roll and yaw. Every camera shutter exposure was precisely logged inboard the INS to extrapolate coordinates and orientation.
A dual frequency base station was also operated during flight operations to be used in the next phase of trajectory processing.
Aerial survey requires precise flight planning to determine where the aircraft and by extension, the camera will be orientated for data capture. This was planned to meet the clients target accuracies of 5cm.
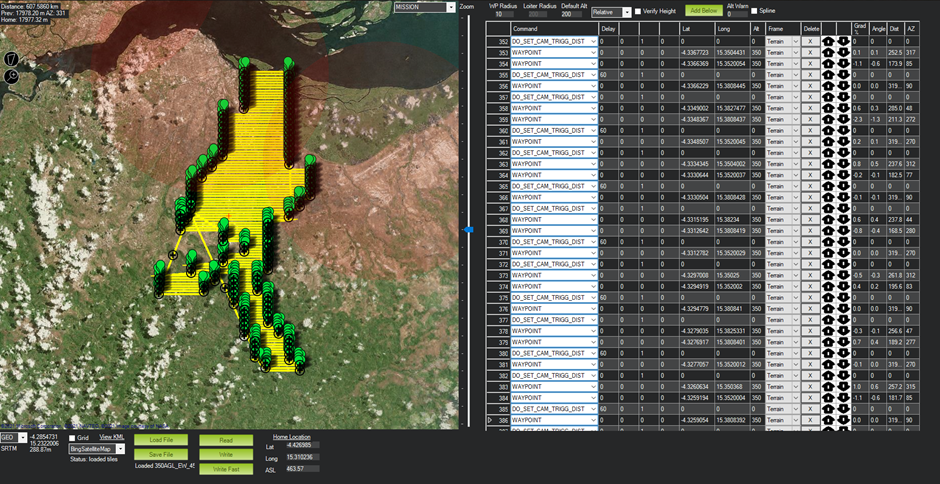
Since the mission is automated, several factors need to be considered such as changes in terrain levels. The aircraft was planned to be operated at certain level above the ground. As the distance between the camera and the terrain change, so does the overlap between images. Retaining the correct overlap between images is crucial for accurate aerial survey. The project was planned for 35% side lap and 70% forward lap.
The trajectories of the aircraft during survey sorties were determined by means of precise point positioning (PPP) and PPK (precise point kinematic) using the dual frequency base station running at the time of data capture. In addition to the position of the aircraft being determined along the flight trajectory, its orientation angles were determined at every point along the trajectory through the use of an inertial measurement unit (IMU). The tightly-coupled GNSS-IMU trajectory was calculated with NovAtel Inertial Explorer.
Using the orientations and GPS-based positions of the aircraft, an accurate image geolocation coordinate list could be generated.



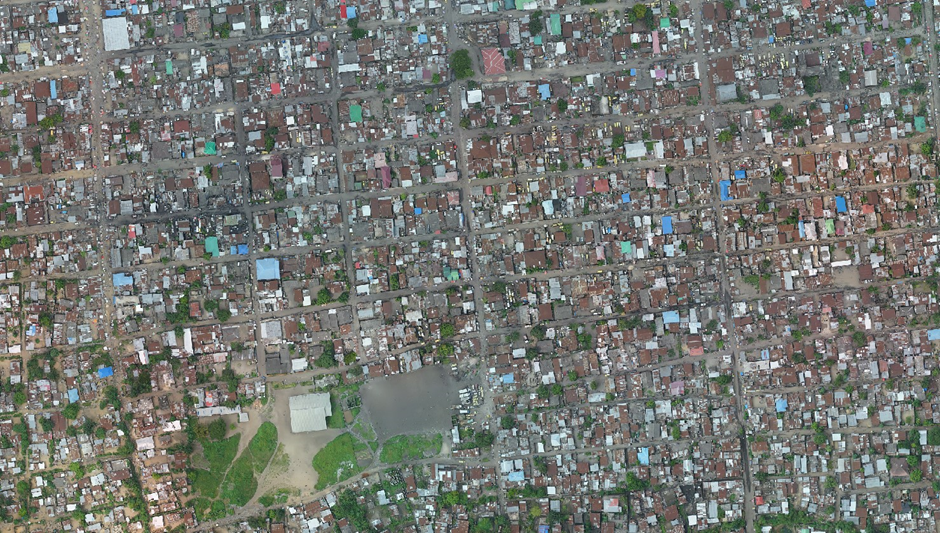
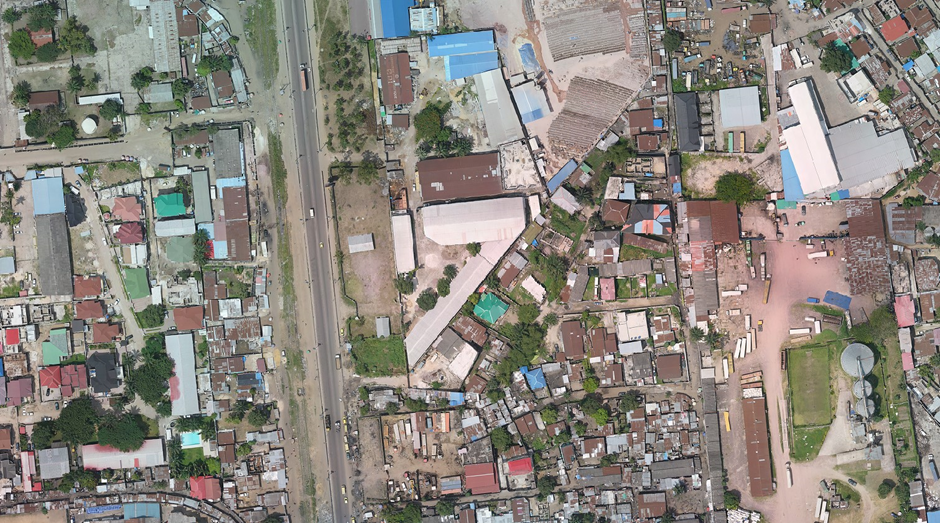
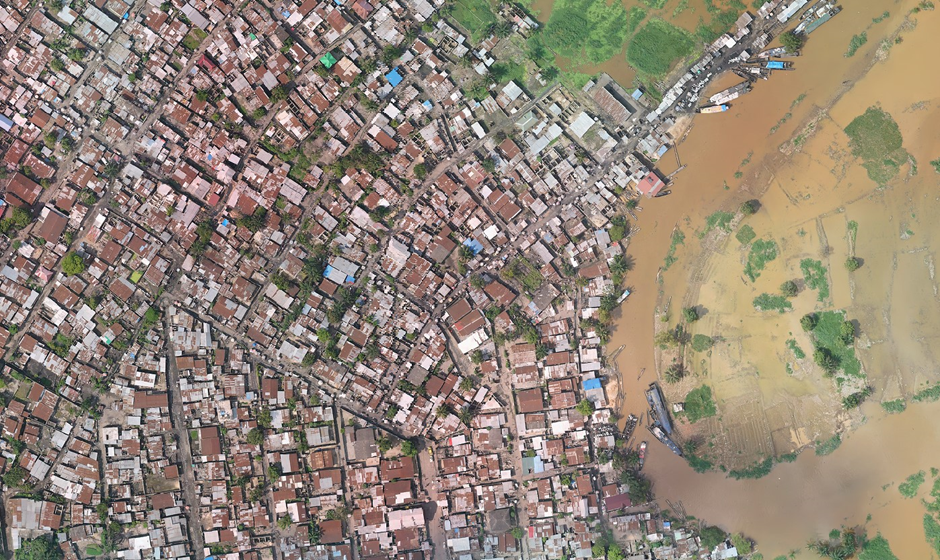
Comments